
Clean Sky 2 Joint Undertaking (JTI-CS2-2014-CFP01-FRC-02-02)
Full Fairing Rotor Head Aerodynamic Design Optimization (FURADO)
Clean Sky 2 – “From break-through technology to full-scale demonstration"
FURADO is part of the Clean Sky 2 program, which can be seen as the continuation of the first Clean Sky Program launched under the EU’s 7th Framework Program of Research and Technological Development (FP7). Clean Sky 2 is dedicated to complete aircraft demonstrators, comprising innovative configurations. Furthermore, this EU program will introduce major demonstrations of several aircraft systems at the aircraft platform level. On the basis of a joint technology initiative (JTI), which is defined by a Public-Private Partnership (PPP) between the European Commission and the European Aeronautical Industry, it is possible to provide the proving grounds for new concepts. The Clean Sky 2 program consists of three Innovative Aircraft Demonstrator Platforms (IADPs), for Large Passenger Aircraft, Regional Aircraft and Fast Rotorcraft. The Fast Rotorcraft IADP consists of two separate demonstrators, the NextGenCTR tilt-rotor and the LifeRcraft compound helicopter.
FURADO – “Direct contribution to the required aerodynamic improvement of the LifeRCraft compound rotorcraft demonstrator"
FURADO is aimed on the numerical design optimization and flow analysis of a semi-watertight full fairing rotor head with respect to drag reduction of a compound helicopter configuration, namely the Low Impact, Fast and Efficient Rotorcraft (LifeRCraft) demonstrator. It has been shown that fully fairing the structural components of the rotor head as a whole provides significant drag reduction potential. The project first phase concentrates on the method development for all consecutive steps. This includes enhancing the existing CFD and optimizer software to be able to automatically optimize the fairing geometries. The software functionality is demonstrated by performing computations of the rotor head blade sleeve fairings, the full-fairing beanie and the pylon fairing for a series of simplified flow conditions. The second phase of the project is dedicated to the pre-development of potential rotor head full fairing configurations. A special focus lies on the preliminary optimization of the blade sleeves, beanie and hub fairing for forward flight conditions with a non-spinning rotor head. The following development phase addresses two tasks. The first task comprises a refined aerodynamic optimization of promising full fairing configurations under the effect of rotor rotation. Flow conditions inside the fairing are also thermally analyzed to avoid any overheating of components. The second task is on wake flow analysis of the drag-reducing full fairing geometries, performing high precision aerodynamic simulations. Strong unsteady air loads on the empennage due to the rotor head wake must be avoided to ensure proper flight dynamics and structural integrity. Consequently, the project results in a seamless integration of the developed software tools into the topic leaders work flow. The complex, CPU-intensive CFD simulations establish a sound database for full fairing rotor head design and analysis, which is not available today.
Description of work
FURADO is designed to last for 48 months and the foreseen work plan is structured in 6 work packages:
WP 1: Project Management, Dissemination and Communication – The project management ensures the timely execution of and reporting on the project. Additionally, it coordinates the communication between the partner and the LifeRCraft project management. The risk associated to each task of the FURADO project will be assessed and feasible risk mitigation measures will be installed if necessary. Finally, all dissemination, exploitation and communication activities will be supervised by the project management.
WP 2: Method Development – During the preliminary phase the tool development for the following optimization tasks is at focus. In agreement with the topic leader the required tool chain for the automated optimization is defined. Based on this input the partner will develop a functional automated optimization scheme and demonstrate its capabilities for a series of representative flow conditions.
WP 3: Preliminary aerodynamic optimization – The preliminary aerodynamic optimization task will be aimed at generating a first set of low-drag shapes. In this context it is also planned to analyze the influence of the rotor head fairing on hover performance. To meet this objective, several intermediate goals have to be achieved. First a 2D automated optimization will be performed to modify thick airfoils, matching the requirements of the blade sleeve fairings. This serves as an input to manually design a 3D blade sleeve fairing. This manual design is than put to test by also performing an automated optimization for the 3D sleeve fairings. Finally, also the impact of the full fairing beanie geometry on both the hover and the forward flight performance is investigated.

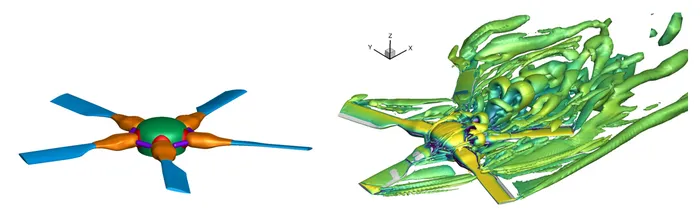
WP 4: Refined aerodynamic optimization – The refined aerodynamic optimization task will be aimed at further optimizing the shape of the blade sleeves and the pylon-fairing. The selected optimized shape combinations are further investigated in different simulation scenarios. Furthermore, the aerothermic risk associated to the full-fairing beanie will be assessed.
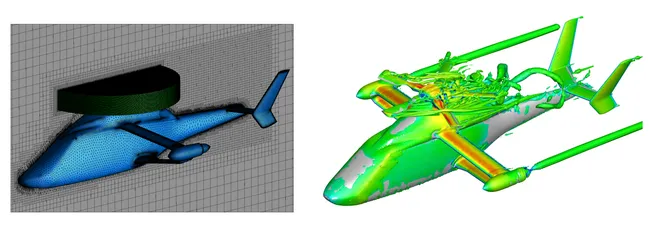
WP 5: Fairings mechanical design – This task is dedicated to the mechanical design of the full fairing elements. The mechanical design will accompany WP 3 to generate a mechanical design of the reference geometry. This design will be updated for the optimized geometry subsequent to WP 4. The mechanical design will be performed in close agreement to the multidisciplinary requirements of the full fairing design, resulting from weight, costs and kinematic boundary conditions. Furthermore, aspects such as safety, maintenance and certification will be considered during the design phase in close collaboration to the project leader.
WP 6: Data exchange and synthesis – Management of the entire data exchange from and to the topic leader throughout the project and seamless knowledge transfer by providing the final synthesis together with the dedicated training of the topic leaders key personnel.
Publications
2017
P. Pölzlbauer, D. Desvigne, C. Breitsamter: Aerodynamic Design Optimization of a Helicopter Rotor Blade-Sleeve Fairing. In: DLRK 2017, German Aerospace Congress, Munich, 5.-7. September, 2017.
2018
P. Pölzlbauer, D. Desvigne, C. Breitsamter: Performance Improvement of a Compound Helicopter Rotor Head by Aerodynamic Shape Optimization. In: 31st Congress of the International Council of the Aeronautical Sciences, Belo Horizonte, Brasil, 9.-14. September, 2018.
Link: https://www.icas.org/ICAS_ARCHIVE/ICAS2018/data/papers/ICAS2018_0070_paper.pdf
P. Pölzlbauer, D. Desvigne, C. Breitsamter: Aerodynamic Design Optimization of a Helicopter Rotor Blade-Sleeve Fairing. CEAS Aeronautical Journal 2018, DOI: doi.org/10.1007/s13272-018-0341-0
P. Pölzlbauer, D. Desvigne, C. Breitsamter: Performance Improvement of a Compound Helicopter Rotor Head by Aerodynamic Design Optimisation of a Blade-Sleeve Fairing. The Aeronautical Journal 2018, DOI: doi.org/10.1017/aer.2018.172
Contact
Prof. Dr.-Ing. habil. Christian Breitsamter
Lehrstuhl für Aerodynamik und Strömungsmechanik
Boltzmannstr. 15
D-85748 Garching bei München
Raum: 1631
Telefon: +49.89.289.16137
E-Mail: christian.breitsamter(at)aer.mw.tum.de