Self-learning control for hydraulic systems
Hydraulic systems, especially in mobile machinery, are omnipresent: in excavators, snow plows, aerial work platforms, loading cranes, agricultural machinery such as combine harvesters, and others, the high power density of hydraulic actuators is used. In addition to high power, high precision is also required, which can only be achieved by closed-loop control. Due to a changing environment, a wide range of applications as well as wear and tear, mobile machinery poses great challenges that push conventional control strategies to their limits.
From a control engineering point of view, the application is divided into a wide variety of fields: unknown and time-varying system behavior requires adaptive/self-learning control for the nonlinear system. The control algorithm must be robust against disturbances and suppress them as far as possible. The handling of several coupled axes falls into the domain of distributed control. Maintaining the flow from pump to tank when the actuator reverses its movement requires switching between valves, resulting in a switching system. Another challenge is the limited availability of sensor technology in the application due to cost and installation space. Not measured variables can be inferred e.g. by methods of virtual sensor technology. Last but not least the safety of the controlled system plays an important role.
In the scope of the AIValve project and in cooperation with the company HAWE Hydraulik and the Institute of Automation and Information Systems, control algorithms are being developed to deal with the challenges of hydraulic systems and to increase precision, speed and energy efficiency.
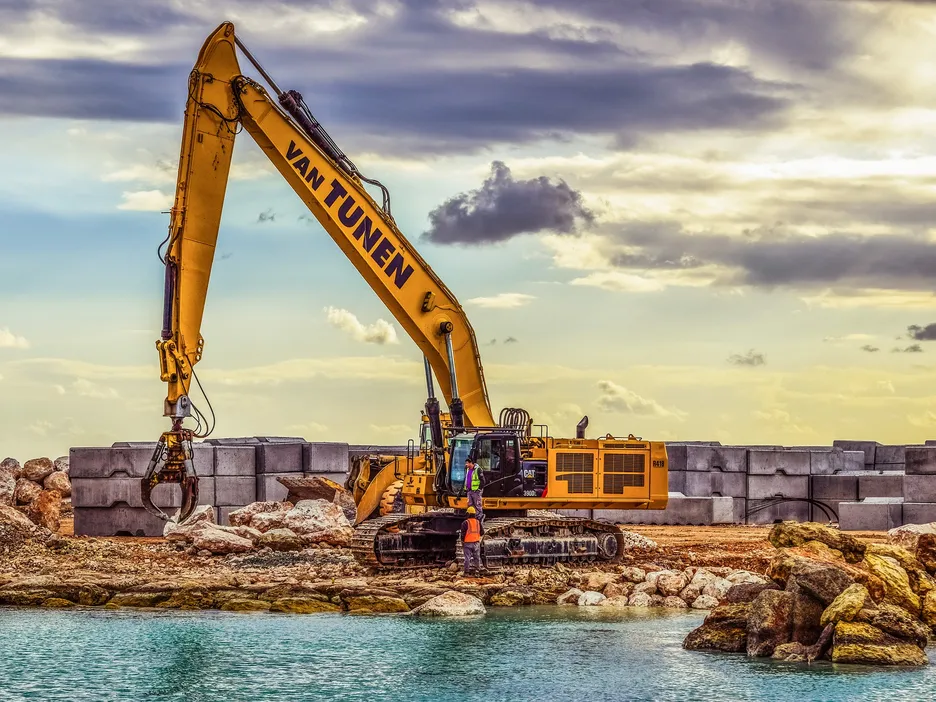