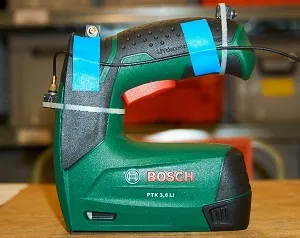
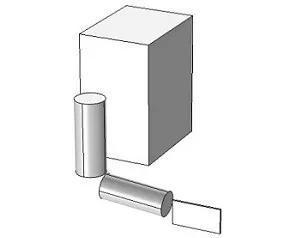
In the course of technization many different mechanical and automatic tools were developed. Along with the obvious advantages though, comes in many cases the exposure of the user to vibrations. Due to the also developing measuring and examination techniques, it has shown that those affect differently varrying parts of the human body. The vibrations can lead to short-term and permanent physical changes and hence to health issues. To avoid these, there are various national and international standards regarding measuring, simulation and the limits for hazard assessment.
In the case of handheld devices the transmission of the vibrations from the handle to the hand and further into the arm depends on several influences. The diversity of the influencing factors pose a challenge for both measurements and simulations. The results of measurements on the device depend among others on the kind and location of the affixing of the sensor and on the vibration characteristics. In simulations and measurements of the transmission of the vibrations to the human hand-arm system its coupling to the device, the body posture while operating it, as well as the rather non-uniform physical properties of the users play a part.
One of the most common approaches to simulate hand-arm vibrations are single- or multiple-degrees of freedom models. The parameters of which are adapted such that the results of the simulation match those of a measurement or measurement series. Due to this origination process their applicability is restricted. Another approach is the use of both the finite element method and multi-body dynamics simulation. Measurements encompass two sub-areas, those determining the vibrations on the device and those looking into the transmission to the hand-arm system of the user. Here accelerometers, laser vibrometers, sensors for temperature and pressure, as well as highspeed cameras are used