
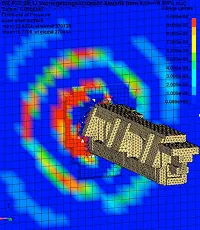


In industrial practice, the new and further development of products often requires a consideration of the vibro-acoustic system behavior. Ideally, the relevant parameters can be determined at an early stage of product development by means of numerical simulation. Here, the velocity pattern of the structural surface serves as an input variable for the sound field analysis. As a result, the model accuracy of the overall vibro-acoustic simulation depends significantly on the quality of the structural dynamic parameters. Accordingly, the aim of our research is to create efficient and reliable methods that increase the model accuracy of a complex assembly. The Finite Element Method (short: FEM) is mostly used as a numerical tool for the description of elastic structural dynamics. Other methods, such as the Boundary Element Method (short: BEM) or the Infinite Element Method (short: IFEM), are appropriate to calculate the acoustic field.
In practical application, it is important to obtain reliable results quickly and efficiently. For this reason, it is our key aim to develop approaches and algorithms that are able to map both linear and non-linear problems as simply and accurately as possible. This includes, for instance, parameter-excited oscillations, material laws of elastomers, friction contacts in joints as well as the transmission behavior of screw connections. As far as possible, the resulting substitute models can be applied - or at least implemented - in commercially available software packages. The quality and reliability of these modelling techniques is finally confirmed by comparison with measurements on the test bench or directly during operation. Furthermore, noise relevant components are identified by means of a Transfer Path Analysis (short: TPA) and their sensitivity is evaluated. A parameter study regarding the element size and the element type is also a subject of these investigations. Depending on the application, the use of a Model Reduction Method (short: MOR) makes sense.