Yan Yan, M.Sc.
Technische Universität München
Lehrstuhl für Thermodynamik (Prof. Wen)
Postadresse
Boltzmannstr. 15
85748 Garching b. München
- Tel.: +49 (89) 289 - 16193
- Raum: 5507.EG.729
- y.yan@tum.de
Research project
Droplet bouncing on heated superhydrophobic surfaces under low ambient pressure
1) Introduction
Droplet bouncing is an important phenomenon that involves complicated physical mechanisms, which is closely related to various applications such as anti-icing, heat transfer and electrical generation, etc.
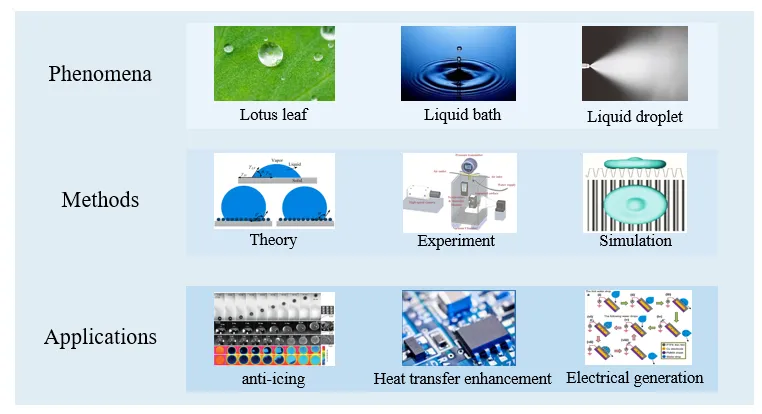
Figure 2 shows the contact process of a droplet impacting on the superhydrophobic surface. The typical bouncing includes the process of spread, retraction and then rebound. The aim of this research is to reduce contact time.
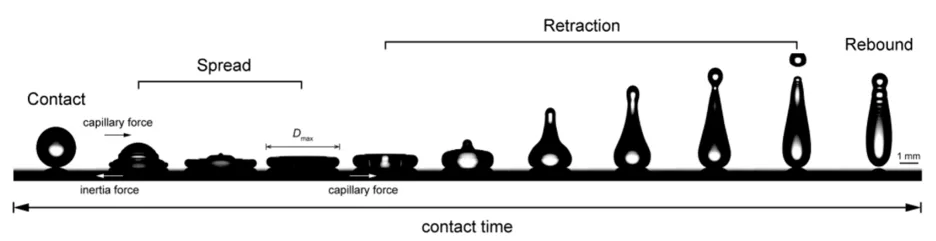
What’s the mechanism behind it to provide the energy or force to make droplet bounce off? Fig3 shows a schematic diagram of droplet impact. When a droplet impacts on the surfaces under normal conditions, an ‘air film’ is often compressed between the droplet and the solid. When the droplet touches the surface, i.e. wetting occurs, a part of the air film is often enclosed in the center of the droplet, which is called ‘entrapped air film’. It may be the air film provides the upward driving force for the droplets to bounce off.
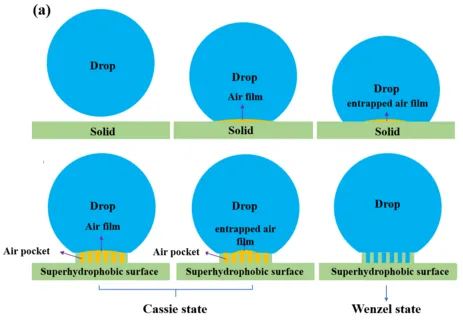
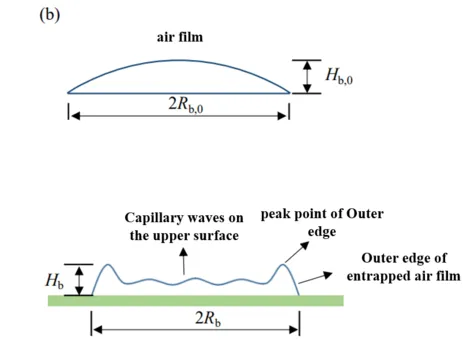
However, when a droplet impact on a hot surface under extremely low-pressure condition, air film involving phase changes will affect the droplet dynamics. An overpressure will be restrained between droplet and substrate because of the rapid evaporation in the micro-channels. This overpressure maybe the driving force that trigger droplet bounce off. When deviating from standard atmospheric conditions, it has rarely considered the influence of the thermodynamic state and composition of the gas layer, especially on the anti-wetting behavior of superhydrophobic surfaces.
So, the focus of this research is to study dynamic behavior of the gas film, figure out how the gas effect make droplet bounce off and finally get the superhydrophobic surfaces design principle under extreme conditions.
2) Procedure and method
2.1) Experiment
2.1.1) Sample preparation
It is planned to fabricate this textured surfaces (10mm×10mm×2mm)- micro-channels and micropillars with 3D printer (S230, BMF, USA). The microscopic scale of the pillars is: [Dp, Lp, Hp]=[20, 60, 40] μm, shown in Fig4(b), where Dp, Lp, and Hp represent the diameter, spacing, and height of the micropillars, respectively.

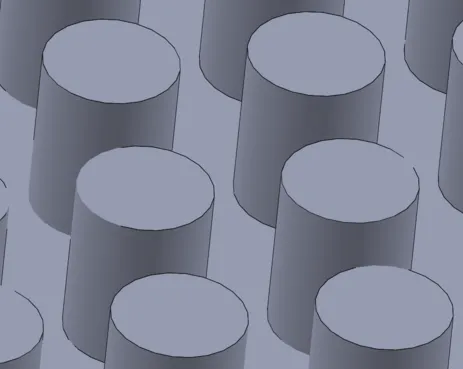
In order to increase surface roughness to get superhydrophobic surfaces, coating is necessary in this work. It is proposed to use fluorosilane -perfluorodecyltrimethyloxysilane (1H,1H,2H,2H Perfluorodecyltrimethoxysilane) for Fluoridation. The static contact angle needs to be above 150° using a drop shape analyzer.
2.1.2) Experimental setup
A Drop Shape Analyzer (DSA100, Krüss, Germany) and a High-pressure Pendant Drop (PD) system are used for this research. Fig5(a) shows different components of PD system, which consists of view chamber, pressure control system, droplet dosing system and electrical heating system. Fig5(b) shows the flowsheet of PD system, illustrating the procedure of how to operate valves to increase pressure, reduce pressure, generate droplet and fill up liquid in the chamber.
(1) About pressure control system, PD system is connected to a gas cylinder-N2 cylinder used in this research. Open the corresponding valve G to allow gas enter. The maximum of pressure is 420bar.
(2) About droplet dosing system, using valve A to allow water in TL1 into minipiston. Handle is used to control the volume of a droplet. The droplet diameter is 2.2, 2.5, 3.0mm respectively in this research.
(3) About electrical heating system, it incorporates a NiCr-Ni thermocouple within the heating jacket to accurately monitor and control the input temperature. The maximum of temperature is 200°C. Besides, the view chamber is outfitted with an auxiliary liquid heating/cooling jacket. This jacket is designed for
connection via a hose to the user's fluid heating or cooling apparatus. The minimum of temperature is -20°C.
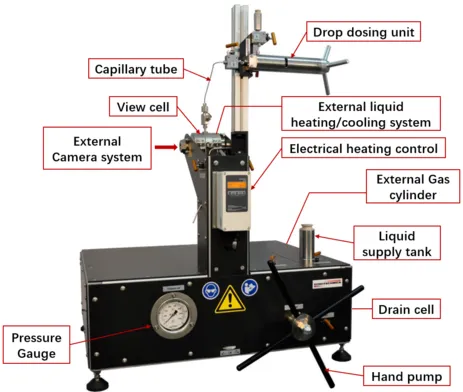
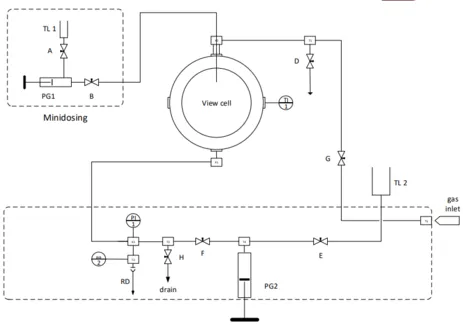
Camera system is provided by DSA setup, shown as in Fig6. The resolution is 2300 fps. The camera can be tilted in order to change the viewing angle of the drop. For contact angle measurements, it is recommended using +2° for sessile drops.
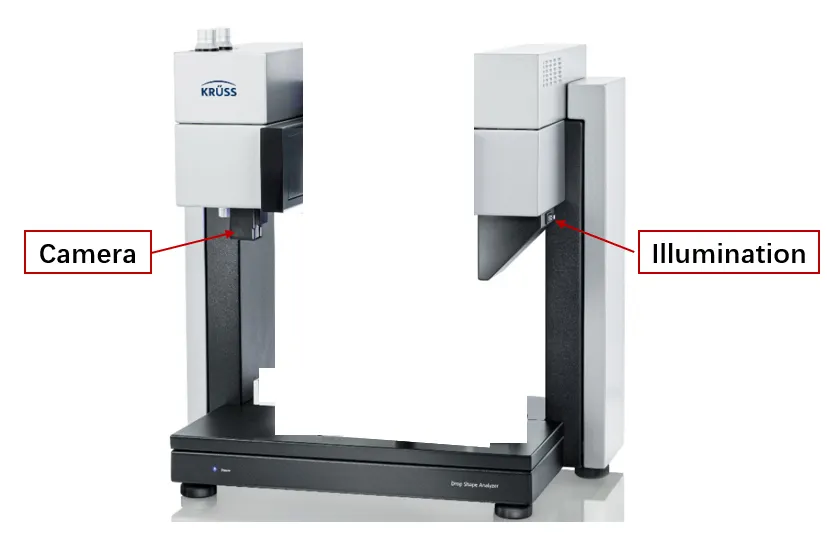
2.2) Simulation
In classic two-phase flow simulation problems, there are often significant differences in the physical parameters between the two phases. Therefore, how to describe the characteristics of the interface between the two phases is a classic topic. It is proposed to use Phase Field Method (PFM) to capture the interface of phase field. In a two-phase flow problem with a three-phase contact line, Navier-slip boundary condition will be added. Besides, In the droplet contact process, it needs to use Dynamic contact angle θd to describe the dynamic process. So PFM combined with slip boundary and dynamic contact angle model method will be used.
Despite the problem of flow field, interfacial heat transfer should be considered due to the rapid droplet evaporation during impact. It consists of a temperature- dependent mixing energy term and a temperature transport equation.
Overall, using combined PFM including slip boundary, dynamic contact angle model and interfacial heat transfer can comprehensively simulate the dynamic behavior of the entrapped gas film.